
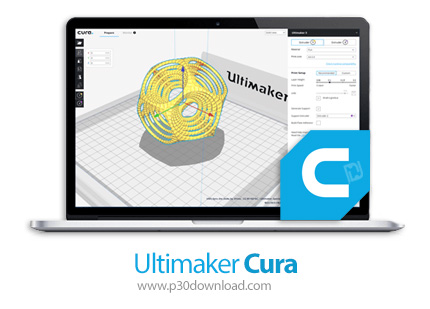
I suppose I'm coming at this feature from the point of view of someone who was debugging an "oozing" problem that occurred after a certain time, so in order to calculate the distance I would need to take the travel speed into account (plus acceleration but maybe not needed for a first-order guess!).

Hi you make a good point - most people will think in terms of distance. It's much easier for the user to set the limit as a distance rather than as a time (IMHO). But you're not going to think, hmm, those travels from one side of the piece to the other should be using retraction, let's set the value to, say, 100mS (or whatever). Hi yes, making it time based could be done as you suggest but do people want to think in terms of time or distance when considering this setting? When you look at the layer view you can see all the travels it is doing and think to yourself, hmm, those travels from one side of the piece to the other should be using retraction but those travels in a small area don't need retraction, let's set the value to, say, 10mm to stop the dribble on the long travels. Couldn't Cura calculate the distance automatically from the travel speed and the time parameter, and generate the appropriate GCODE to implement that? Setting it as a distance means that it will need to be adjusted if travel speed is changed. However I have to ask - why is it distance based? Shouldn't it be time based? The most common case, I imagine, is what I've described above, and this "oozing" effect is dependent on travel time not travel distance. This feature will help a lot if I need to keep Combing enabled. I have a complex shape that the head takes too long to navigate while travelling in Comb mode, and the molten filament dribbles out before it gets there, leaving a large gap at the same place for each layer. Having encountered the perfect scenario for this new feature, I am thankful.
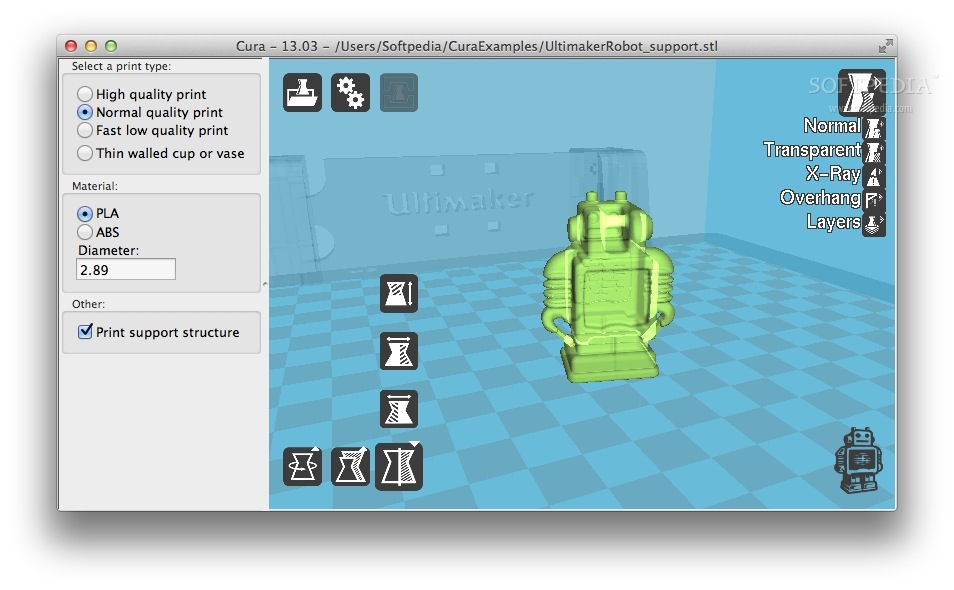
When set to a non-zero value, combing travel moves that are longer than that distance will use retraction, to maintain optimal nozzle pressure for better print quality. It will be live and you can ask any questions to our CTO, Miguel Calvo.Max combing distance with no retract.
#ULTIMAKER CURA 3.4 FREE#
We’re hosting a free tech demo on February 7.
#ULTIMAKER CURA 3.4 1080P#
Reliable bed tilt compensation (no more thumbscrews) 2.4 and 5 GHz Wi-Fi A 1080p camera (mounted higher for a better view) Compatibility with 280+ Marketplace materials Compatibility with S5 project files (no reslicing needed) And a whole lot more The UltiMaker S7 also includes quality of life improvements:

We also reversed the front fan direction (fewer plastic hairs, less maintenance), made the print core door magnets stronger, and add a sensor that helps avoid flooding. This effectively makes it much harder to not achieve a perfect first layer, improving overall print success. The re-engineered print head has an inductive sensor which reduces noise when probing the build plate. Along with that, 4 pins and 25 magnets make it easy to replace the flex plate perfectly – even with one hand. But we also don’t recommend using or adhesion structures for UltiMaker materials (except PC, ’s PC). Not only do you not need tools to pop a printed part off. A PEI-coated flexible steel build plate makes a big difference to productivity. The build stack has also been completely redesigned. To further enclose the build chamber the S7 only has one magnetically latched door. This filters the exhaust air of every print and also improves build temperature stability. It now includes an integrated Air Manager. The UltiMaker S7 is built on the success of the UltiMaker S5 and its design decisions were heavily based on feedback from customers.
